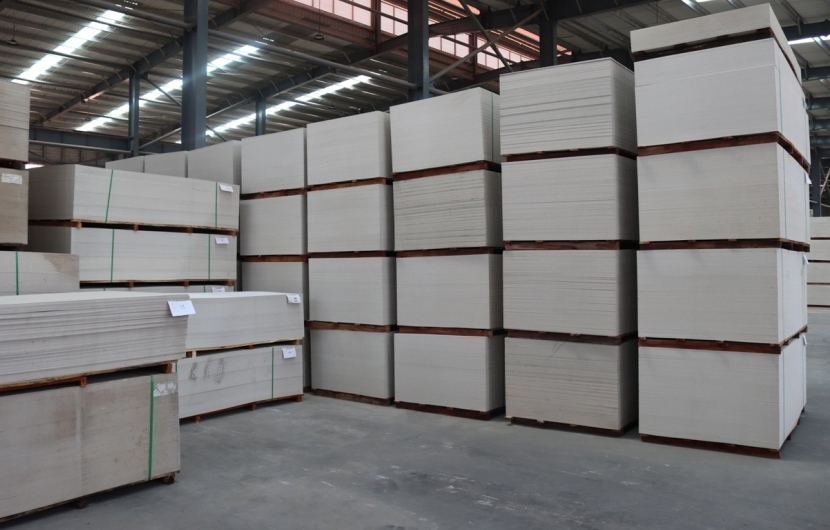
Product Description
Fiber cement board is created by using siliceous-calcareous materials as the principal cementing ingredients and loose, short fibers like cellulose or inorganic mineral fibers as reinforcing elements to create calcium silicate cementing bodies through pulping, molding, and autoclave curing.
A typical cement board was no longer created by the autoclaved reaction of cement and siliceous elements in the raw ingredients. It overcomes the disadvantage of easy drying and shrinkage of typical cement products while inheriting the benefits of waterproofing and anticorrosion of cement. It is a brand-new building material with a broad range of applications and exceptional performance.
By carefully combining wood fiber, cement, quartz sand, and other ingredients, molding with the flow slurry method, pressurizing the mold, maintaining the pressure, and performing other fully automatic processes, the NMNC asbestos-free reinforced calcium silicate board/fiber cement board (ultra low density, low, medium, and high density) is green, energy-saving, fireproof, and waterproof building wall material.
Due to its exceptional qualities, including its ability to be green, energy-efficient, environmentally friendly, light weight, and high strength, it can be painted with environmentally friendly materials, or decorative materials like composite facing paper and aluminum plate can be sprayed on the surface to create a composite decorative plate, and thermal insulation materials like composite rock wool can be sprayed on the back to create an integrated thermal insulation and decoration plate. This is commonly done in order to decorate buildings.
Manufacturing Process
Fibre Cement Boards are manufactured using the Hatschek process, which involves several laminations of slurried mix or core ingredients on a large steel cylinder known as the 'BOLE' (with a specific embossed pattern for Designer Boards). When the desired thickness is achieved, the 'green/wet' board is cut and put on a conveyer where it is trimmed to size and then stacked and left for a short period of pre-curing.
The final curing is done through autoclaving that involves High Pressure Steam Curing (HPSC). This hydration process changes the chemical structure of the cement/silica and quarts and selected mineral fibre matrix to produce a highly durable and versatile fibre cement buidling board. After autoclaving, the boards are allowed to go through a short stabilization period to bring about equilibrum with the ambient moisture content a controlled environment.
Product Application & Uses
Ceiling system
Partitioning system
Wall Cladding
Sidding
Flooring
Fascia
Parapet
Interior wall decoration
Exterior wall decoration
Product Advantages
Asbestos free
Water resistant
Fire resistant
Shatter resistant
Termite resistant
50 years guarantee
Technical and Physical Specifications
Fibre cement boards are manufactured using state-of-art manufacturing process using basic mix of raw materials cement, cellulose pulp fibres and additives. Raw materials composition for each batch board is controlled using Microprocessor Based Batch Controllers and Programmable logic controllers. The boards are manufactured in various thickness ranging from 4mm to 24mm with the help of Online Thickness Control System.
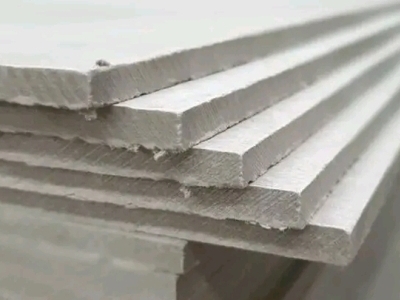
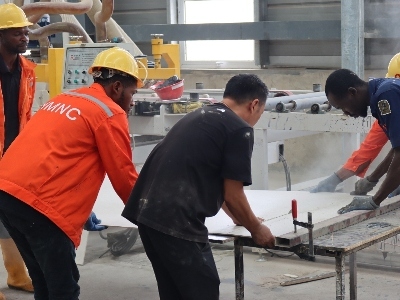
Standard Size
Length: 1220mm
Width: 2440mm
Thickness range: 4mm - 24mm
Physical Properties.
Flextural Strength (along and across the fibre)
Modulus of Elasticity (along and across the fibre) 8726.3 N/mm3 and 6557.2N/mm3 respectively
Adhesion (bond) Strength, average 15N/mm3
Screw Withdrawal Strength (Perpendicular and parallel to the surface) - 1243.2N & 791.2N respectively
Compressive Strength, average - 2.6 N/mm3
Apparent density - 1.33 kg/m3
Storage
Our boards should be always be carried on long edges (width wise) by atleast two persons to avoid damage to the board and excessive strain on people handling them.
While loading and unloading the board, it should be lifted by at least four people to support the four corners.
Maximum two to three sheets should be handled for thickness of 6mm or less. For thickness higher than 6mm, single sheet should be handled at a time.
During transportation, the boards should be stacked flat, edges and corners should be fully protected and adequate packing material should be used at both bottom and sides
Dirt settling on the textured surface of boards while cutting, sawing and screwing should be avoided.
Boards should be handled with gloves or by applying French chalk to avoid spoiling of the primer or making a patch mark.
Handling
Boards must be stacked horizontal, never inclined, on a smooth and leveled surface, preferably 6 inches to 8 inches above the levelled surface.
While loading and unloading the board, it should be lifted by at least four people to support the four corners.
Boards should always be stored under adequately ventilated covered space without allowing direct exposure to sunlight, rain etc. in case of non availability of covered space, board should be covered with polythene sheets and must be stacked on pallets with proper stretch wrapping to protect from weathering forces.
If boards get wet or damp due to wrong storage then it should be dried out in natural conditions before further handling. In any case, boards should be installed in position within 2-3 weeks of procurement.
Boards should be stacked to the maximum height of 3 feet or 1 meter per stack
Adjacent stacks should be with minimum gap of 1 feet or 300mm.
Safety and Emvironmental Protection
When fiber cement board goods are cut, they will release dust that can be inhaled. Human health will be harmed and may possibly be harmed by inhaling these dusts. As a result, the following warnings need to be taken into consideration in the plate processing room.
The workspace must be maintained adequately ventilated, and it should be set up outside or somewhere where there is good air circulation.
The processing site must be cleaned with a vacuum cleaner or water sprinkler, and the cleaned dust must be put in a waste bag.
As much as possible, use power tools with suction functions.
Operators must put on a dust mask and safety eyewear.